We’ve been around the block. Stone Aerospace founder Dr. Bill Stone began designing mission-driven equipment for expeditionary exploration over forty years ago. Discover our history with this quick tour down the trail of invention that followed.

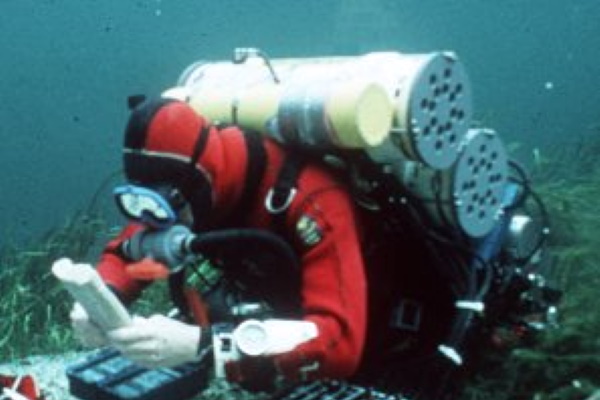
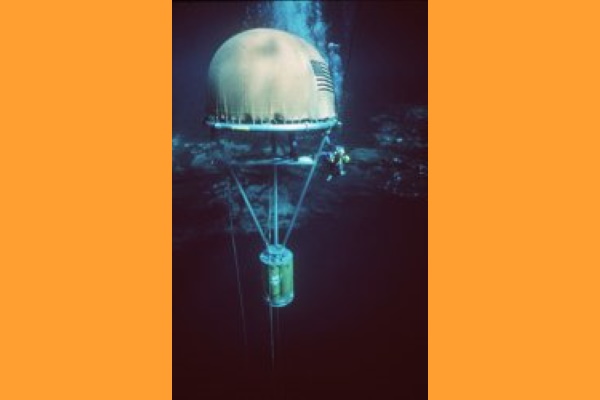
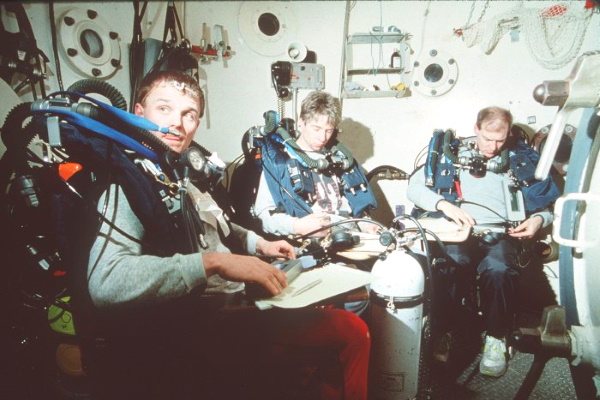
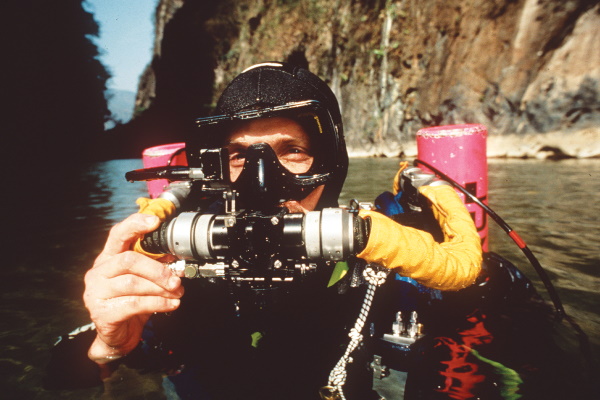
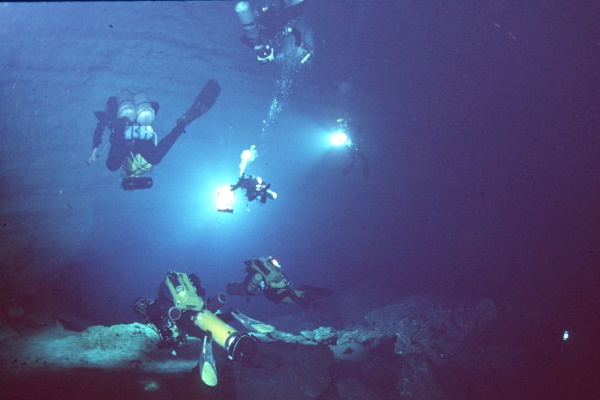
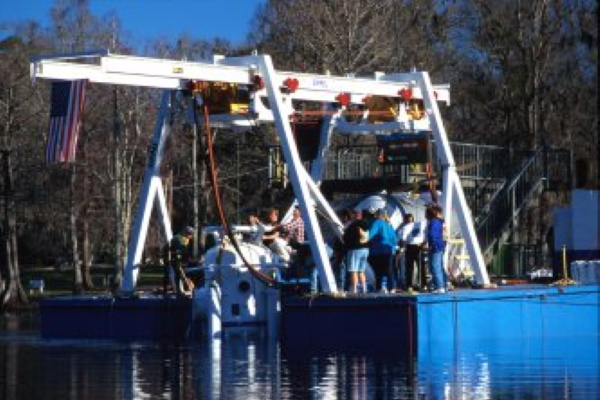
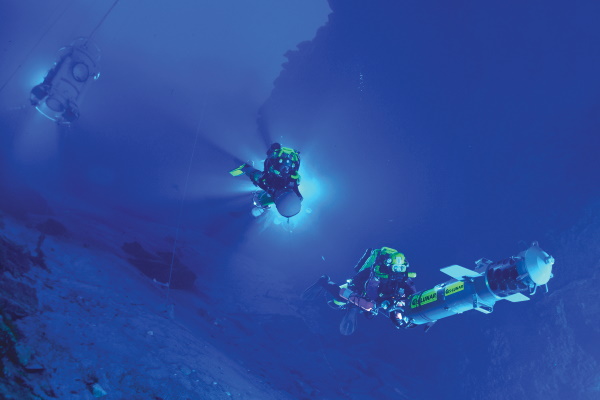
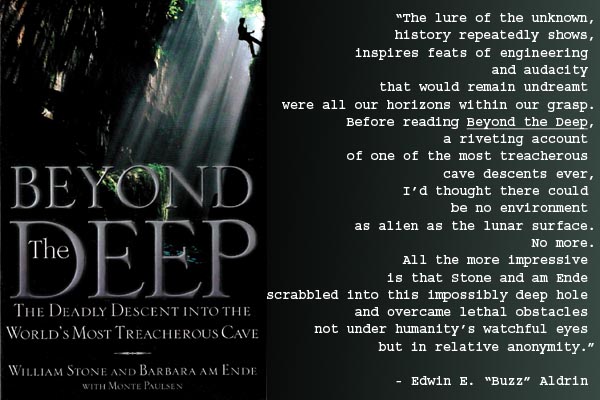
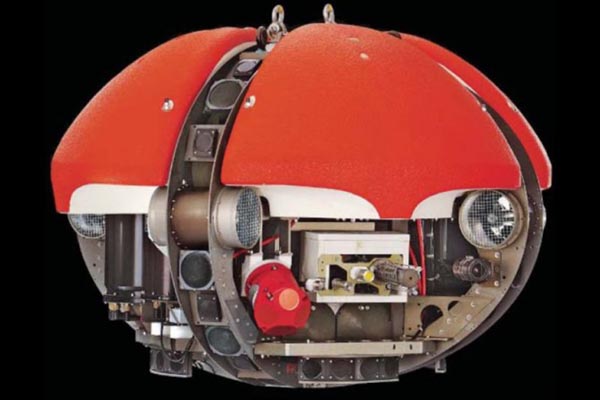
1980 High Pressure Life Support
When exploration of the extraordinarily deep (-1475 m) system of caves on Mexico’s Huautla Plateau hit an underwater tunnel at the -1353 m level, the U.S. Deep Caving Team (USDCT) was stopped by the limits of existing technology—metal diving tanks of sufficient range were too heavy to transport down the 3,000 meters of ropes that were rigged to reach the flooded tunnel. Stone led the development of the first high pressure composite Scuba system in the fall of 1980. Working with Acurex-Aerotherm, the NASA Crew Systems Division, and Sherwood-Selpac, the engineering team developed a 400 bar rated S-glass/epoxy tank that carried 2600 liters of compressed air and weighed only 8.3 kg. Regulators and valves were developed specially to handle this pressure and were among the first to employ DIN style captured o-ring designs for safety. The USDCT team used this in 1981 and in 1984 to explore more than 2 kilometers of underwater tunnels inside the Huautla Plateau.
Although much more efficient PLSS systems were later developed the USDCT has continued to use high pressure technology for short reconnaissance diving in remote locations. The photo above shows Bill Stone (left) and Tommy Shifflett — the two test divers for the composite equipment in 1980 — together at the J2 expedition basecamp in the Ocotal cloud forest in southern Mexico in 2005. The tanks shown here were upgraded to carbon-epoxy to achieve the same performance capacity but at only 4.3 kg unpressurized weight.
NEXT >
1984 Cis-Lunar MK1
During the expedition to Huautla’s Peña Colorada (“Red Wall”) cave the team used 72 of the composite tanks to reach the limit of exploration, 9 kilometers inside the mountain. At that point all 72 tanks were expended and had to be laboriously hauled to the surface following each mission. Navy commander John Zumrick, who was a member of the expedition, mentioned in a meeting at basecamp that alternative life support designs existed. Stone subsequently spent three years (1984-1987) researching first the Navy MK16 rebreather and then the NASA shuttle spacesuit PLSS designs before rejecting both as being unsafe for use in the hazardous “overhead” rock flooded tunnels of Huautla (where one could easily be two to three hours from a tunnel containing air) before deciding to invent a mission-specific device. The apparatus that resulted, the Cis-Lunar MK1 rebreather was revolutionary on several fronts. It was the first truly “redundant” PLSS in that it had twin, independent closed-cycle gas processing “stacks” to recycle exhaled air as well as the important distinction of being able to “cross route” gas and consumables supplies while on a mission.
It was also the first diving apparatus to ever use anhydrous lithium hydroxide (LiOH) as its mechanism for carbon dioxide removal. LiOH is dangerous stuff. If it becomes wet the exothermic reaction is so strong that it can produce a steam surge in the apparatus along with caustic chemicals that could severely injure or kill the user. To prevent this Stone designed a hydrophobic membrane separator system. The rig had four onboard computers (two for each half) and a predicted range of 24 hours underwater. On December 3rd and 4th, 1987, Stone (above, reading a paperback in Wakulla Springs, Florida) spent 24 hours continuously underwater with only the MK1 PLSS to keep him alive. Amazingly, the dive was conducted using only half of the consumables available — meaning the MK1 could have been used to remain underwater for two full days.
< PREVIOUS | NEXT >
1987 Variable Depth Habitat
While the testing of the MK1 took place at Wakulla Springs, Florida in the fall of 1987 a parallel project was underway to extend knowledge of the deep flooded aquifer that fed the artesian spring. Closed cycle PLSS technology was not far enough along to be used for these exploratory missions, which used high pressure metal and composite tanks (above) carried on propelled “sleds” that carried each member of a 3-person exploration party. Maximum length missions of 80 minutes were conducted to distances from the entrance of 1,400 meters at 90 meters depth. At that point the dive teams were facing between eight to 10 hours of decompression in the chilling water. Recognizing this logistics problem in advance, Stone began designing a variable depth underwater habitat to receive the returning dive crews and to allow them to slowly ascend to the surface in dry comfort as they paid their decompression penalty. The result was funded by Rolex USA, and was fabricated by the Sippel Company of Pittsburgh, PA to Stone’s designs. The hemispherical crew quarters was 3 m in diameter and could house up to six in an emergency. The design was counter-ballasted to within 1 ton of upward buoyancy. It was then controlled by a 40 m hand operated chain hoist. CO2 gas (from metabolic exhalation) was purged using a surface supplied low pressure, high volume compressor and medical grade redundant zeolitic filter system. Pure oxygen K bottles (green tanks) provided open circuit oxygen at depths above 10 m. Fire hazard was prevented by the surface air purge system.
< PREVIOUS | NEXT >
1988-1993 MK2 Through MK4
The MK1 testing at Wakulla Springs had shown the amazing promise of a fully-redundant closed cycle PLSS for long range exploration. The “Cis-Lunar” prefix which Stone had given to the device was carefully chosen (and trademarked). The term specifically originates in the aerospace world. At the time Stone was working at NIST on efforts to boost the space shuttle external tank to orbit and to convert it to an orbiting industrial workshop. Working with orbital mechanics calculations daily, he became aware of the term “cis-lunar” which was used to describe the locus in space for the earth-moon system defined by the five Lagrangian stabilization points. It was within this volume of space that the first fledgling commercial manned space efforts were likely to take place. Considering that developing (and using) equipment for lunar exploration was his long-range objective, Stone founded a company, in 1987: Cis-Lunar Development Laboratories, Inc. The MK1 was viewed as a prototype for the type of design one would want in a long range industrial spacesuit PLSS.
Aside from this historical footnote, the MK1 weighed in at 90 kg and was not suitable for terrestrial exploration. Over the following five years three generations of redundant closed-cycle PLSS backpacks were developed and tested, culminating in the MK4 design. This was a 9 hour range depth-independent design with three onboard processors, head-up display, redundant mixed-gas supplies (both heliox and oxygen). It was rated to 200 m underwater and included an integrated real-time decompression engine that was parallel-processed across the three computers. Extensive manned testing included hyperbaric chamber simulations (above, showing, left to right, Ian Rolland, Rob Parker, and Dr. Noel Sloan at the IUC facility on City Island, NY).
< PREVIOUS | NEXT >
1994 San Agustín Expedition
The purpose of of the MK4, and the reason for the sustained R&D effort, was to equip a team for a major exploration assault on the underwater tunnels at -1353 m in the Sotano de San Agustín, on Mexico’s Huautla Plateau. Previous efforts with high pressure open circuit composite systems had reached the limits of that technology in large “going” tunnels. Only a radical technology advance could open that frontier. Equipped with nine MK4 rigs, an international team of 44 explorers, led by Stone, arrived on the Huautla plateau in February of 1994. During the course of the following 4-1/2 months the team explored to a depth of -1475 m (at the time, the 4th deepest point reached by humans inside the planet) and a distance of 7 kilometers from the nearest entrance. Importantly, 600 meters of that distance, beginning at the -1353m level, was through a 30 meter deep underwater tunnel. A total of 22 MK4 missions were conducted during the expedition, many with return-to-safe-haven times exceeding 90 minutes. During the entire project only 1400 liters of oxygen and 2500 liters of heliox gas were used. (Read more at the San Agustín expedition page at the USDCT website.)
The expedition itself was epic in scale and drama. National Geographic Magazine carried a feature story on the project in their September 1995 issue. The MK4 PLSS had proven itself to be remarkably survivable. From a technical standpoint one of the most impressive incidents of the expedition occurred when the lead team of Bill Stone and Barbara am Ende were returning from Camp 6 from the 7-day final push. As they were gearing up and into their pre-dive checklist, the main programmable display on Stone’s MK4 went dead. In the process of descending 92 shafts and traversing 3,000 meters of ropes the rebreathers had taken an incredible beating. The cable leading to Stone’s display had partially unscrewed. This was enough to allow a few drops of water to enter the LCD unit electronics and short it out. This, however, was not the end of the story. After performing a self-diagnostic test the remaining two onboard computers detected the problem, voted the wrist display unit out of the system, and took control. The head-up display flickered momentarily and came up 4×4 green, an indicator that all systems were up and running on automated closed-cycle control. The return dive was conducted without further incident.
< PREVIOUS | NEXT >
1995-1998 Cis-Lunar MK5 and the Fat Man
The technical success of the MK4 on the San Agustin Expedition attracted both scientific and commercial interest in the following years. The expeditionary MK4 units were used by Bishop Museum in Hawaii to discover more than 200 species of previously unknown fish down to depths of -200 meters in the south Pacific, a zone previously uninvestigated because it was too deep for normal Scuba and too shallow for those paying day-rates for use of research submersibles. It also attracted the attention of venture capitalists. With the infusion of significant capital Cis-Lunar expanded to a staff of 10 and established a manufacturing plant in Massachusetts. It also acquired the underwater communications firm DiveComm and the joint company began a process of developing new products for underwater exploration.
The flagship product was the next generation Cis-Lunar MK5 closed-cycle PLSS. Three years of R&D and advances in electronics and fabrication technology allowed for dramatic improvements in the design, particularly from the user interface, gas routing, and field maintenance standpoint. Importantly, the MK5 was a manufactured commercial product. Through 1999 a hundred units were sold world wide, mainly to scientific, cave, and deep wreck divers as well as underwater photographers, owing to the lack of bubbles and noise. In parallel, a 20 kilometer range underwater propulsion vehicle, known as the “Fat Man” was developed for long range missions to be conducted in Wakulla Springs, Florida in 1999. It used an aircraft alloy hull rated to 200 meters depth and state-of-the-art nickel metal hydride 100AH batteries. It had a variable speed control, a safety kill switch, a backup direct-power switch, and a top velocity of 2.5 knots (1.4 m/s) towing a heavily-laden exploration diver.
A special dual MK5 was developed for the 1999 National Geographic expedition to Wakulla that had a range of 18 hours. A typical exploration and mapping team (above, at -80m) in addition, carried redundant propulsion systems. This extraordinary combination of technology allowed exploration teams to routinely log missions of up to 5 hours inside the springs. These were at depths of 95m and distances of up to 4 km from the entrance with 2.5 hour return “drives” to return home. They still had waiting of up to 19 hours of decompression. Following the expedition both designs were marketed. Sales, however, were low due to the high cost of manufacture.
< PREVIOUS | NEXT >
1998 Mini Sat System
Realizing that extraordinary decompression times would be involved with the 1999 project at Wakulla Springs Stone Aerospace (newly founded in 1998) began design of a modular floating “mini-sat” decompression system. Wakulla Springs, as part of the Florida parks system, had firm rules restricting the nature of what could be done at the spring in terms of industrial equipment being on site. It was thus proposed, and accepted, that a modular self-contained floating facility would be permitted. It could be constructed on the water in just a single day. The resulting design utilized three crane-deployable micro-barges, a hyperbaric chamber, a transfer capsule, and a custom designed dual gantry crane with redundant man-rated hoists. During actual missions the “bell” was pre-staged at -30m. Following a typical 4 to 5 hour in-water decompression following a 4 to 5 hour bottom time exploration mission, the away teams would lock into the bell and be transferred to the surface.
Their arrival was tracked on closed circuit video cameras beginning at the -60 m level. Meanwhile, support teams carried their PLSS backpacks up independently. Then they interrogated them with a laptop computer. Finally they used a custom-written program to take the individual diver’s tissue tensions and generate a chamber decompression profile.
This was the first time such a real-time decompression management system had ever been deployed. Once on deck the transfer capsule was mated to the hyperbaric chamber. The pressures were then equalized. The crew could change out into dry clothing and relax. It would be 12 hours before the hatch could be opened. Surface crews rotated out each 4 hours to operate the chamber, maintain oxygen partial pressure, and vent CO2. A total of 32 exploration and mapping missions were successfully conducted using this system with no bends incidents.
< PREVIOUS | NEXT >
1999 Digital Wall Mapper
The greatest challenge to understanding the nature of a subterranean labyrinth, particularly one filled with poor visibility water, is that of the creation of a map. The State of Florida and National Geographic Society were interested in building a true, three dimensional map of Wakulla Springs. If successful, it would be the first time such a map had ever been created in any cave. Certainly it would be the first of one that was 95m deep and filled with tannic-laden water with 5-10m visibility.
Stone Aerospace set out to develop an instrument that could mount as a front module to an existing underwater propulsion system and automatically create a 3D map of it’s environment as it was driven through the subterranean water-filled tunnels, some of which proved to be in excess of 50 meters in diameter. The result was based on three unusual concepts. First, having an inertial guidance unit with known drift characteristics. Second, using a massive sonar array. Third, using a magnetic location system. These could be integrated to build the 3D map as a team of divers was piloting their vehicle into unexplored territory.
The mathematics and instrumentation developed validated the concept with registration errors being reduced to half a meter one sigma. A total of 50 kilometers of tunnel mapping was conducted during the 3 month project.
More information on the Digital Wall Mapper
< PREVIOUS | NEXT >
2002-2004 Beyond the Deep and NGL
Periodically all pioneers must take time to reflect and document what has been accomplished. Following two years of writing Time-Warner books published the book Beyond the Deep, which chronicled the 1994 San Agustin Expedition. Apollo 11 astronaut Buzz Aldrin’s review validates the growing appreciation that the subterranean world represents the last great exploration frontier on this planet.
Similarly, following two years of writing, NISTIR-7117 appeared in May of 2004. This was primarily authored by Bill Stone while working at NIST. This seminal work represents the state of laser radar technology at that time. It is still a useful reference that is loaded with background physics and ladar optics information. Download it here free.
< PREVIOUS | NEXT >
2004 DepthX
Following the National Geographic Society expedition to Wakulla Springs in 1999 it was clear that the technology and design architecture of the Digital Wall Mapper could be used for a lot of interesting spin-off concepts – both for underwater AUVs and, as well, for UGV and UAV systems with real-time LADAR being substituted for the sonar arrays. One of those brainstorming concepts was that there was sufficient local processing and imaging power (the Digital Wall Mapper had eight onboard computers) to build a fully autonomous underwater mapping robot—one that required no pilot. In fact, such a concept had been discussed in the workup to the Wakulla project. However, it was thought to be less technologically risky to have a human at the wheel. Now, attention returned to the idea of a fully autonomous device. Two proposals were written, jointly with the University of Texas, in 2001 and 2002 to the National Science Foundation. Both proposals were turned down. Not long after that, Dr. Dan Durda, working at Alan Stern’s outfit (Space Science and Engineering Division, SwRI, in Boulder, Colorado) learned of a research opportunity from NASA. They were seeking concept development ideas for how to handle one of the most audacious exploration projects (human or robotic) ever planned: the sub-surface exploration of the hypothesized ocean of the Jovian moon Europa. Dr. Durda, who was also an underwater explorer, knew of the work at Wakulla Springs and contacted Bill Stone. Stone Aerospace (as PI) and SwRI jointly wrote a proposal, along with Carnegie-Mellon University and the University of Texas at Austin. It was to develop a prototype for the Europa lander third stage. The “hydrobot” would cruise the sub-surface ocean in search of the first life found off Earth. NASA did not accept the proposal. The team re-grouped, additional co-investigators were brought onto the team, and and the proposal was re-written. NASA approved funding in October of 2003 and work formally began in April of 2004.
Read about DepthX and all our subsequent projects on our projects pages.
< PREVIOUS